In this quick project, I worked backwards, by using the already thought-out concept from my Light Pack project, to improve upon the look and material of the product and match it to a desired aesthetic and sustainable concept. I learned a great deal about KeyShot and Photoshop during this assignment.
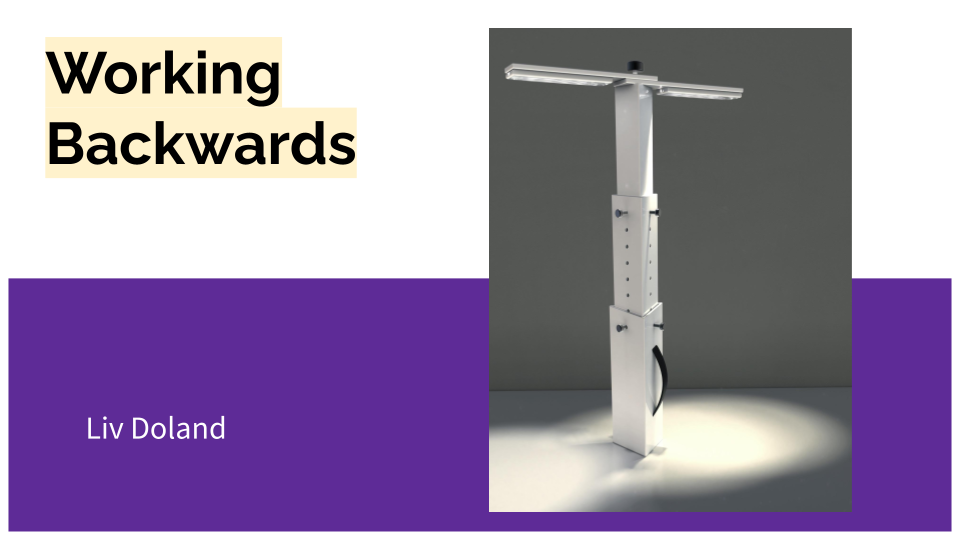
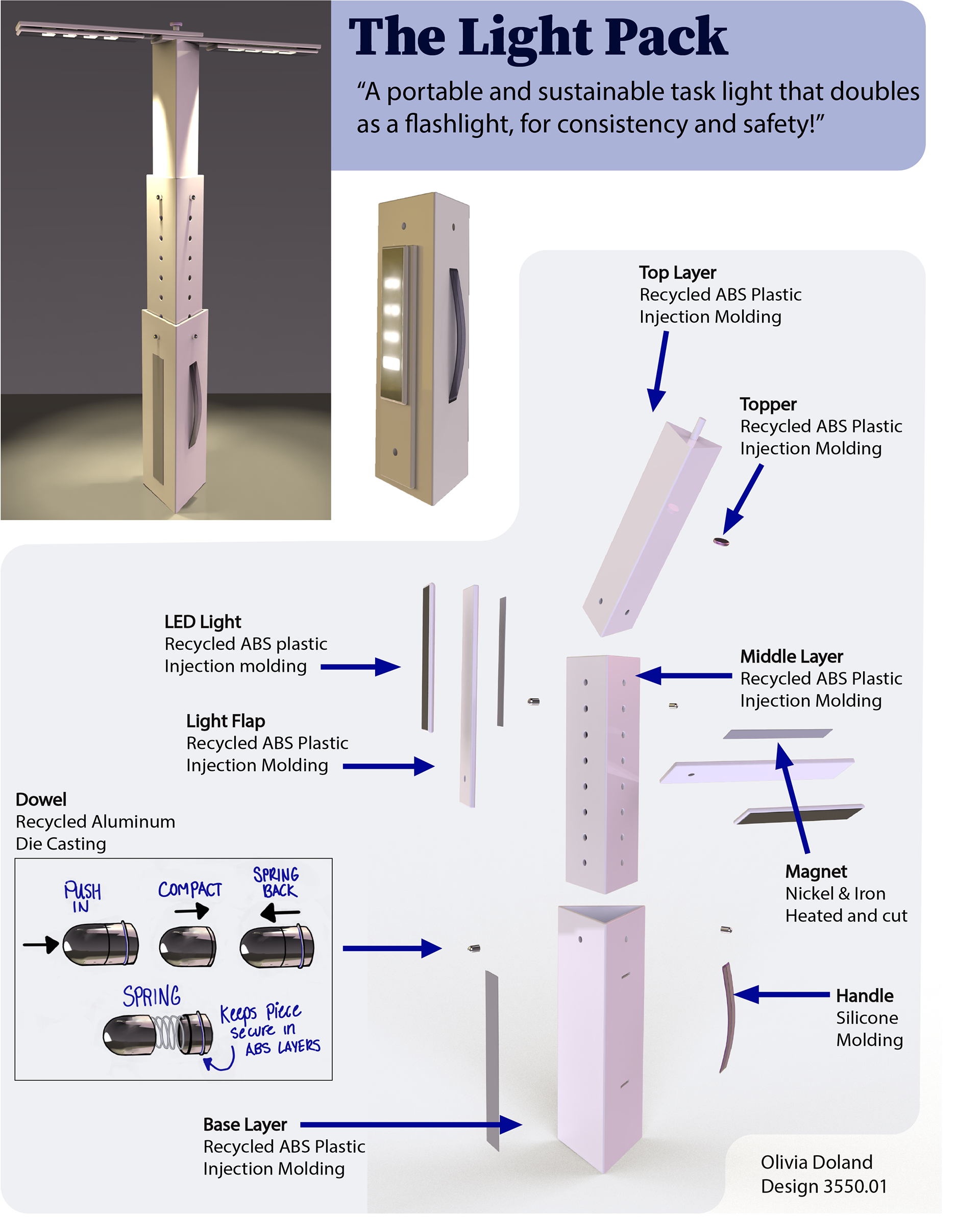
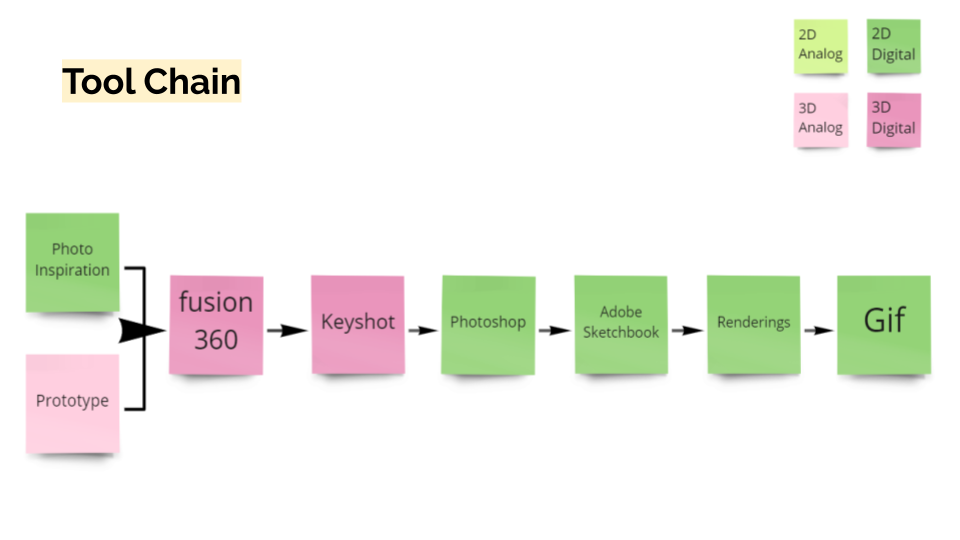
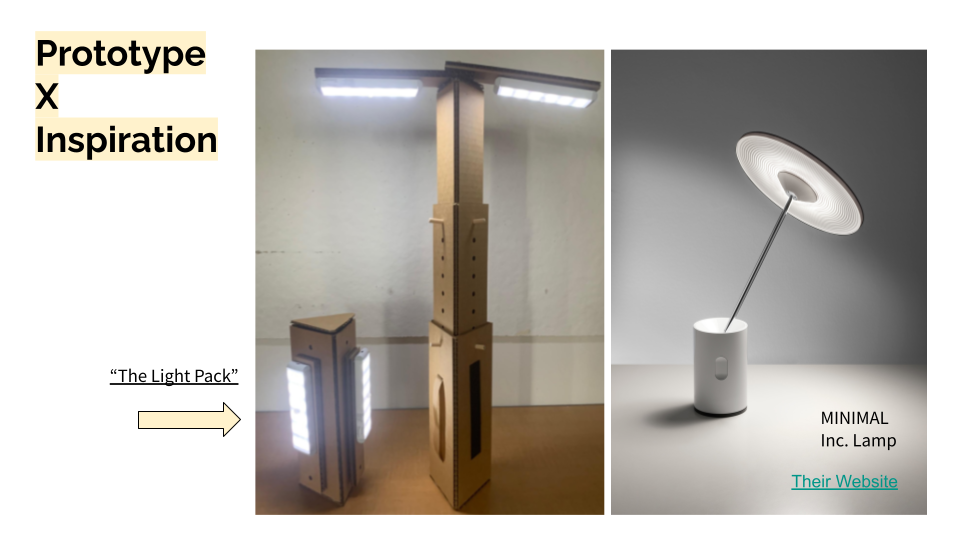
Inspired by the Minimal Inc. Lamp aesthetic: https://www.mnml.com/sisifo
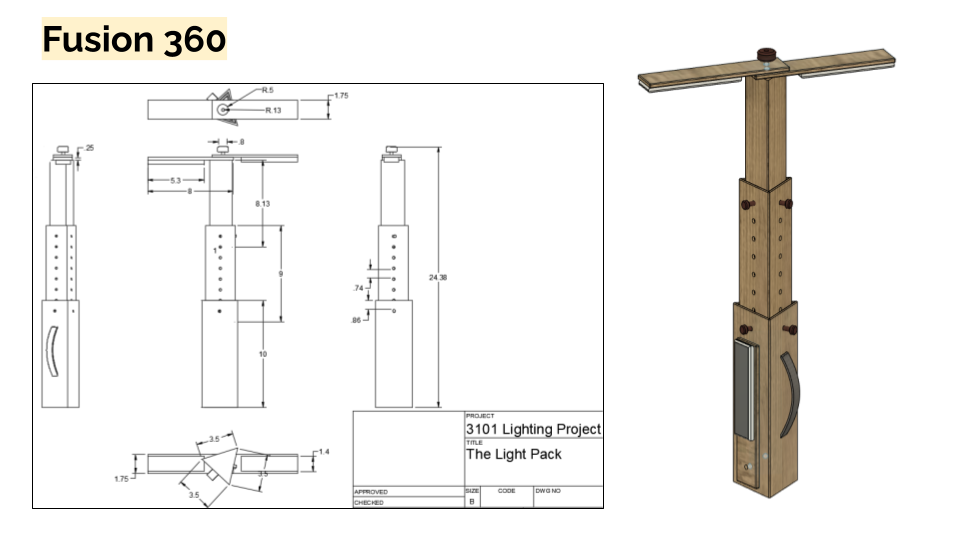
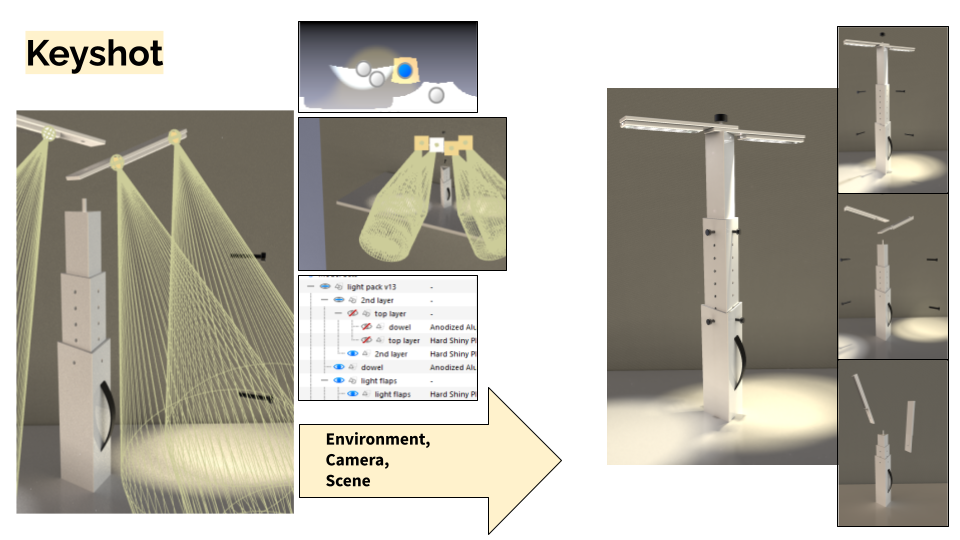
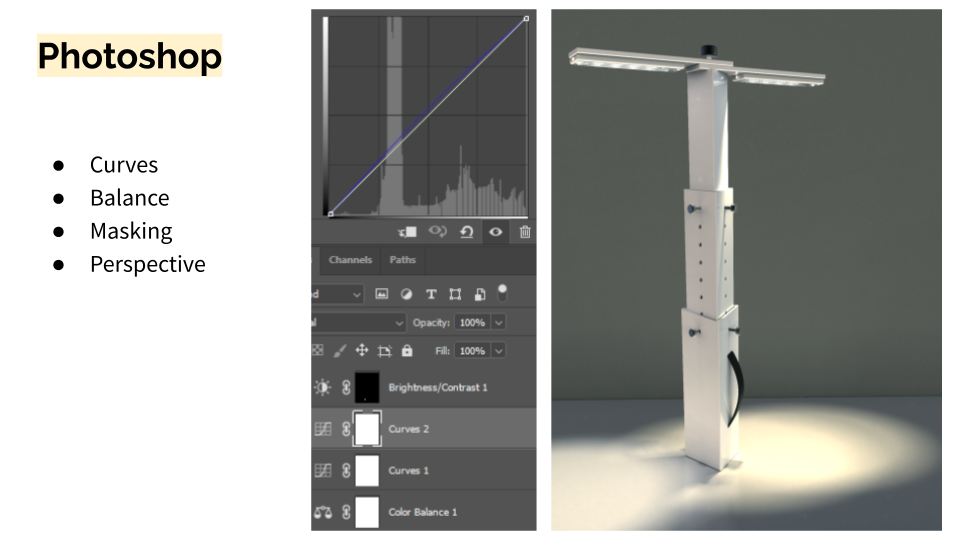
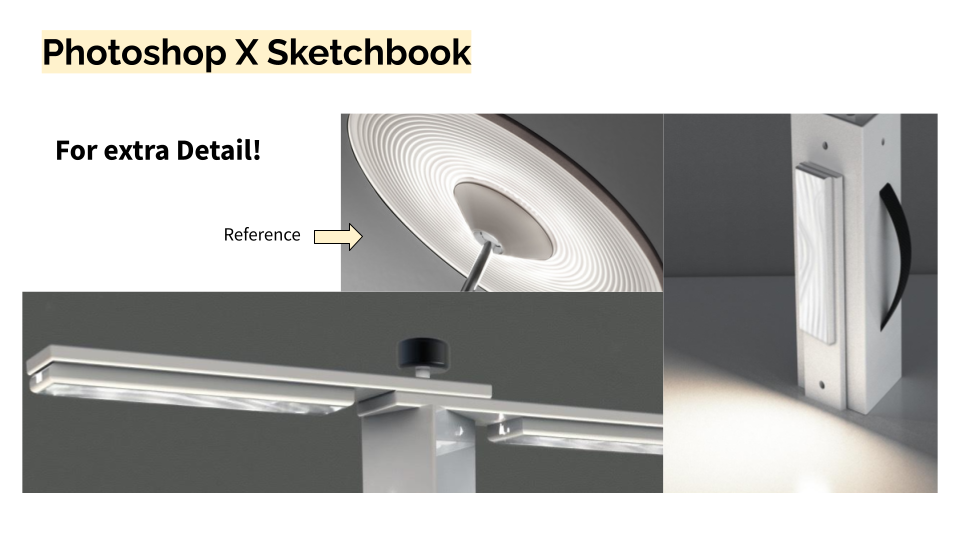
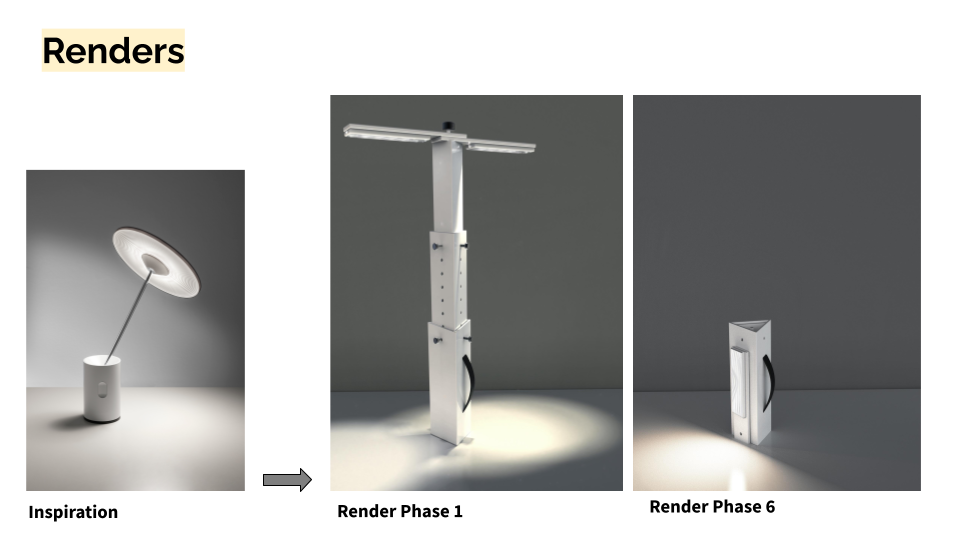
Light Pack Redesign Reflection
I chose to redesign the light pack I created first semester because I noticed an opportunity to make many improvements to both the design and its materials. The concept I came up with during the fall was a battery powered LED task light that utilizes the same mechanism as a telescope to compact and become portable. The lights would be able to attach the compact version and serve as a flashlight while the user is moving from one place to the next. The portability of the light allows for consistent lighting in any setting, and a sense of safety in the dark. After presenting this project to my peers in the fall, I realized there were multiple aspects I would like to change about it.
First, I wanted to alter its materiality. The prototype I had originally made for this project truly did function, but it was only made of cardboard, which is not very durable. This product would need to be made of materials that can sustain lots of use, and endure constant transportation, as well as several types of weather. In addition, it was important that the materials be sustainable beyond enduring lots of use, they should be designed with thoughts of repair and with consciousness of our environment. Also, it was necessary for the materials to be as light weight as possible, so it is easy to carry the light from one place to the next. Therefore, after much consideration, I decided to have the main bodies be made of recycled ABS plastic. The strap would be made of recycled silicone, the magnets of nickel and iron (of course) and the dowels/mechanisms for compacting the model would be made of recycled aluminum!
The recycled ABS plastic would provide for a lightweight light pack compared to other denser materials such as metal, and wood. In the beginning, I wanted the light pack to be made of wood, but I realized this would not sustain well in different indoor, outdoor temperatures, especially if it rains. So, using plastic would be more durable than materials like wood that do not last as long in different climates. Using recycled ABS would require melting down already used plastic to prevent using unsustainable processes to create new plastic. This is a good way to keep resources in a closed system and prevent plastic from being trashed in our oceans and landfills, when it can be melted down, injection molded and put to better use. Injection molding allows the melted plastic to be injected into molds that fit the exact forms of the light pack, so it can be mass produced without wasting any excess materials. In addition, the molds allow for various parts to be made fast and separately, so that if one part of the light pack were to break, a person could buy that piece on its own instead of having to buy a whole new product and waste materials.
The recycled silicone handle would utilize the same melting, molding, and closed system process. I chose to have the handle be made from silicone for the smooth, ergonomic comfort it provides for the hand, making it easy to carry from one place to the next. Next, I chose to redesign the mechanism for compacting the light. Originally, I was going to utilize wooden dowels to hold the expanded light in place. The dowels could be easily moved to adjust the height or compact the form into a flashlight. However, after changing the material of the light pack to recycled ABS plastic, I recognized an opportunity to make the mechanism with less material, so it is cheaper, more light weight, and less parts to move around. I studied the ways that telescopes, and modern-day suitcase handles move, to come up with new “dowels.” These would be made of recycled aluminum which is easily melted down and die casted to be mass produced into the pill-like shape I had imagined. It utilizes a spring in the middle, so users can press the “dowel” form in and adjust the height of the task light. Altogether, the aluminum provides for a sleek finish, with functional light weight form, taking the light pack to the next level.
Finally, I chose to utilize magnets to attach the lights, instead of the Velcro from my
original prototype. The magnets hold their form much longer, whereas Velcro starts to fall apart after prolonged use. Overall, I am thankful for the opportunity to get to learn and understand more about materials and their production mechanisms this semester because it helped me rethink the design of my light pack and improve it!
original prototype. The magnets hold their form much longer, whereas Velcro starts to fall apart after prolonged use. Overall, I am thankful for the opportunity to get to learn and understand more about materials and their production mechanisms this semester because it helped me rethink the design of my light pack and improve it!